Current projects in Shake and Break Research Group
Low Cycle Fatigue and Creep Behavior of High Entropy Alloys (HEAs)
Members: Dayane Oliveira, Mingwei Zhang
Fatigue of materials is a topic of concern for the design of components that are subjected to cyclic loads due to the fact that those loads can lead to catastrophic failure. In this context, low cycle fatigue (LCF) tests are useful in examining aspects of structural evolution that inform about damage accumulation and fatigue crack initiation. In addition, strain rate change tests reveal information about the kinetics of dislocation motion and interactions that govern the cyclic strength of metallic materials.
Dayane’s research projects focus on understanding the mechanisms of cyclic deformation using the techniques mentioned above in two different materials. The first one is the CoCrFeMnNi composition within the Multi-Principal Element Alloys (MPEAs), and this is a collaboration with Oak Ridge National Laboratory. The novelty of these new alloys and the limited amount of work published about their fatigue behavior allow for fundamental research to be performed. The second material is 316L stainless steel, commonly used for hydrogen services. This project is a collaboration with Sandia National Laboratories, Livermore, and the goal is to understand how hydrogen affects the LCF performance and the dislocation motion in this steel.
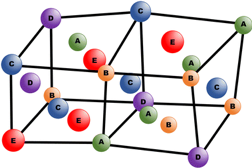
(Source: MacDonald et al. 2017.)
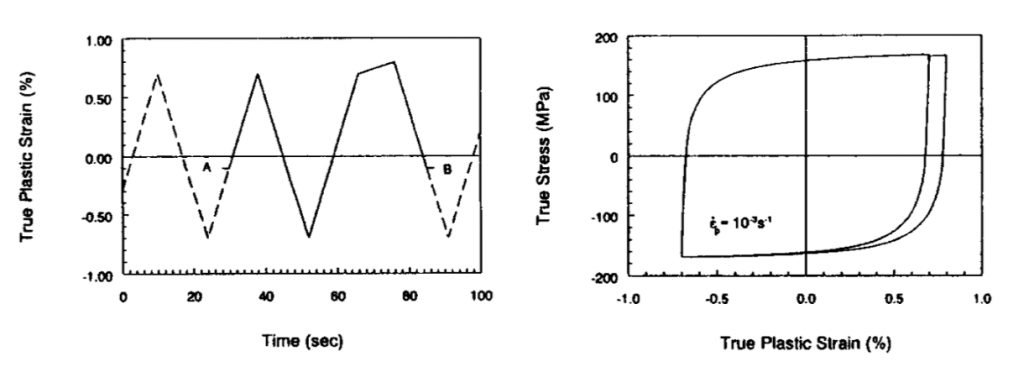
(Source: Kaschner & Gibeling, 1996.)
The creep behavior of materials becomes significantly more important at higher temperatures > 0.5Tm. Mingwei’s current research focus is the steady-state and transient creep behaviors of a high-entropy alloy, CrMnFeCoNi, and its underlying deformation mechanisms. Understanding deformation mechanisms for structural materials at high temperatures and being able to predict their behaviors play critical roles in the progress of developing new creep-resistant materials. In addition, stress change tests working as a mechanical probe of deformation are highly desired since materials are constantly subject to changing loads in real scenarios, and dislocation kinetics needs to be investigated in both equilibrium and non-equilibrium conditions. They are especially effective for studying HEAs whose deformation mechanisms are still unclear.
Mingwei’s long-term research objective is to integrate mechanical testing, advanced characterization, and multiscale computation to establish new or modify current physical-phenomenological models that predict the mechanical behavior of emerging complex alloys at a variety of stress and temperature ranges that meet the need for specific applications. In addition, the physical processes accompanying deformation will be considered and elaborated in those models, including but not limited to the nature of dislocations, the evolution of grain structure, dislocation substructure, material/phase stability, and most importantly, dislocation interactions with the matrix, grain or phase boundaries, solutes, and/or particles.
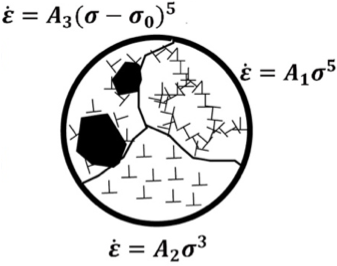
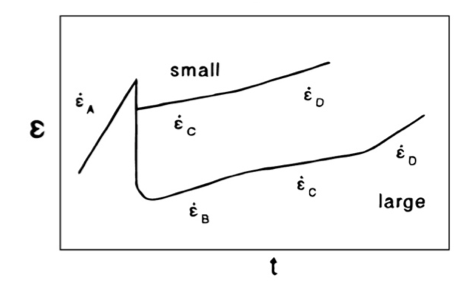
(Source: Broyles, 1995.)
Fatigue Crack Growth of Additively Manufactured (AM) Materials
Member: Christine Smudde
Direct energy deposition (DED) is an additive manufacturing process that can produce complex near-net shape metallic components in a single manufacturing step. DED additive manufacturing has the potential to reduce feedstock material waste, streamline manufacturing chains, and enhance design flexibility. A major impediment to broader acceptance of DED technology is limited understanding of residual stress and microstructure in components produced by DED. A design choice as simple as changing the build orientation has been observed to result in differences as great as 25% in yield strength for type 304L austenitic stainless steel deposited with otherwise identical deposition parameters.
Fatigue addresses the effects of cyclic loading on a material, which is important when considering the life of structural components. Christine’s research focuses on fatigue crack growth rates in metals after initial crack nucleation. She is currently working with additively manufactured 304L stainless steel in collaboration with Sandia National Laboratory, California. These metal components, which are made using the direct energy deposition (DED) and powder bed fusion (PBF) technologies, are machined into fatigue crack growth compact tension specimen (C(T)). To better understand the role of residual stress and microstructure on fatigue behavior in DED 304L, specimens were extracted from both vertical and horizontal orientations relative to the build direction. Using a constant delta K method, she intends to explore the intricacies of fatigue crack growth in AM materials in their different orientations by using FCG to probe the complexities of their microstructure and their residual stress variations.
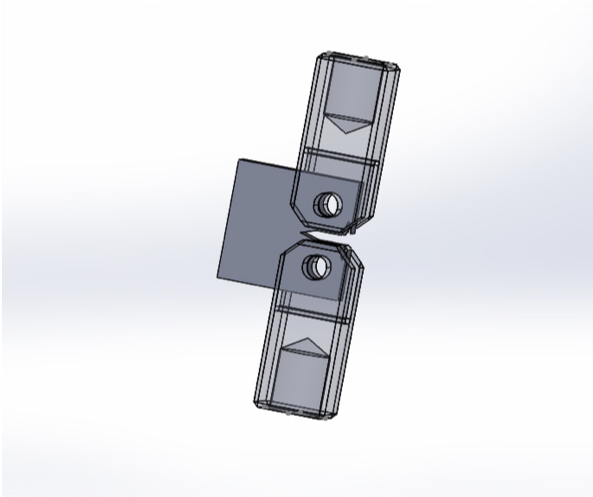
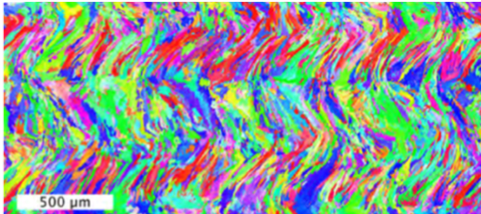
(Source: Smith, Sugar et al. 2017)
Remaining Life Calculations and Crack Growth Rate for Various Forms of Stress Corrosion Cracking as a Function of Temperature
Member: Jeffery Lord
In industry, there are several corrosive environments that can cause steel to crack. The likelihood of cracking and the speed at which cracking occurs is a function of the material microstructure, concentration of the corrosive component, pH, temperature, and stress intensity at the crack tip from tensile and residual stress. Jeffery is researching the mechanisms of various forms of stress corrosion cracking (SCC), including Chloride SCC of Stainless Steel, Wet H2S Sulfide Stress Cracking of Carbon Steel, Caustic SCC of Stainless Steel and Carbon Steel, Carbonate Stress Corrosion Cracking of Carbon Steel, and Amine Stress Corrosion Cracking of Carbon Steel.
The focus of Jeffery’s research is determining the effect that temperature has on the crack growth rate of these various forms of SCC. Crack growth rates from the literature will be used to calculate the effect of temperature on the remaining life of pressurized equipment containing cracks in various SCC environments. Remaining life will be calculated in a series of comparative case studies using a fracture mechanics approach based on API RP 579 Fitness-for-Service Section 9 Level 3 assessment methodology and SCC crack growth rates reported in literature. This comparative study will be a useful tool for industry to promptly assess the complex problem of SCC to determine the appropriate time for repairing and replacing equipment containing stress corrosion cracks in various corrosive environments and temperatures.
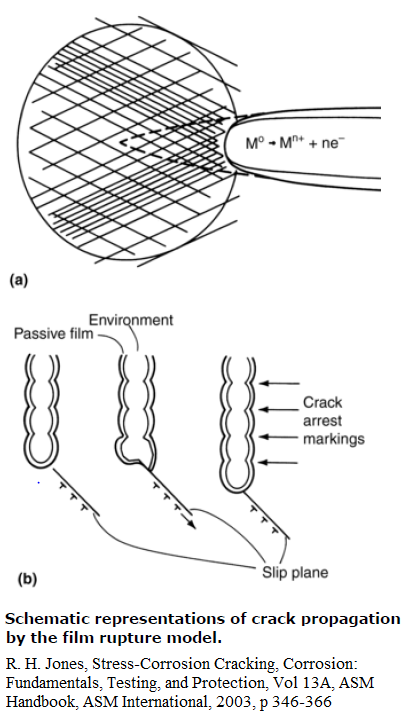
Creep Properties of an Additively Manufactured Oxide Dispersion-Strengthened (ODS) NiCoCr Multi-principal Element Alloy
Member: Gianmarco Monfared
Multi-principal element alloys (MPEAs) offer an excellent solution to the challenge of maximizing strength and ductility in structural materials. However, conventional manufacturing methods and subpar high temperature properties have limited the range of applications of MPEAs to date. One promising approach to overcome these limitations is to use additive manufacturing (AM) as a means to introduce a uniform distribution of dispersoids to increase the high temperature capabilities of the MPEAs. Accordingly, Gianmarco’s research focuses on the creep properties of dispersion strengthened (DS) MPEAs. The DS-MPEA NiCoCr with nanoscale yttria (Y2O3), designated ODS-NiCoCr, is used in this study because there is a reasonable degree of understanding of this system from previous work. However, the knowledge gained from Gianmarco’s research will be applicable to many DS-MPEA systems. The materials used in this investigation will be manufactured using selective laser melting at NASA Glenn Research Center. Precise measurements of creep rates under constant-structure conditions will be used to find the Helmholtz free energy of activation and activation areas for dislocation motion at various stages of creep deformation. Gianmarco’s objectives for this study are to obtain conclusive high temperature creep data for a DS-MPEA, to develop a fundamental understanding of the mechanisms that control high temperature deformation in DS-MPEAs, and to determine how AM affects the properties of ODS-NiCoCr.
The Relationship between Residual Stress, Manufacturing Processes, Bearing Life and the Microstructural Change that Occurs
Member: William Bania
Compressive residual stresses play an important role in the life of the bearing from preventing the initial crack formation to slowing down the crack propagation that leads to spalling. Current bearing design models do not account for various levels of compressive stress nor is there enough data to support how bearing B10 life is affected by different residual stress profiles. Often engineers are faced with the situation where a manufacturer produces a product that does not fully meet a requirement. This is often the case with residual stress. It is not only difficult to accurately measure but the acceptance values are not always based upon process capability nor practically achievable values. Through my research I will develop a relationship between the bearing B10 life and the compressive residual stresses; showing the relationship of both the magnitude of the stress and the need for a minimum value of residual stress at given depths.
As part of this investigation the microstructural changes that occur during rolling contact fatigue which lead to crack formation and eventual spallation will be analyzed. The use of TEM and SEM to investigate these changes will lead to an understanding of the mechanism of the microstructural decomposition or alteration.
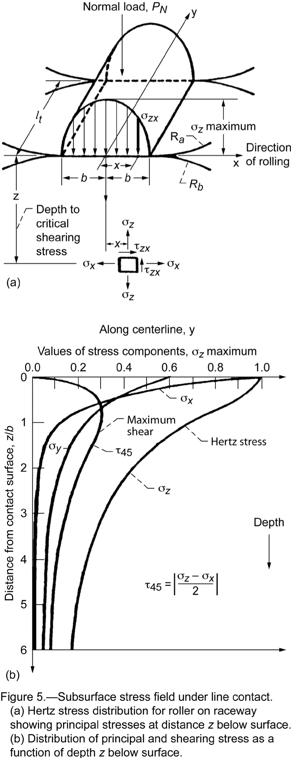